メタルマスクの加工について
2023年02月27日時点の情報です。
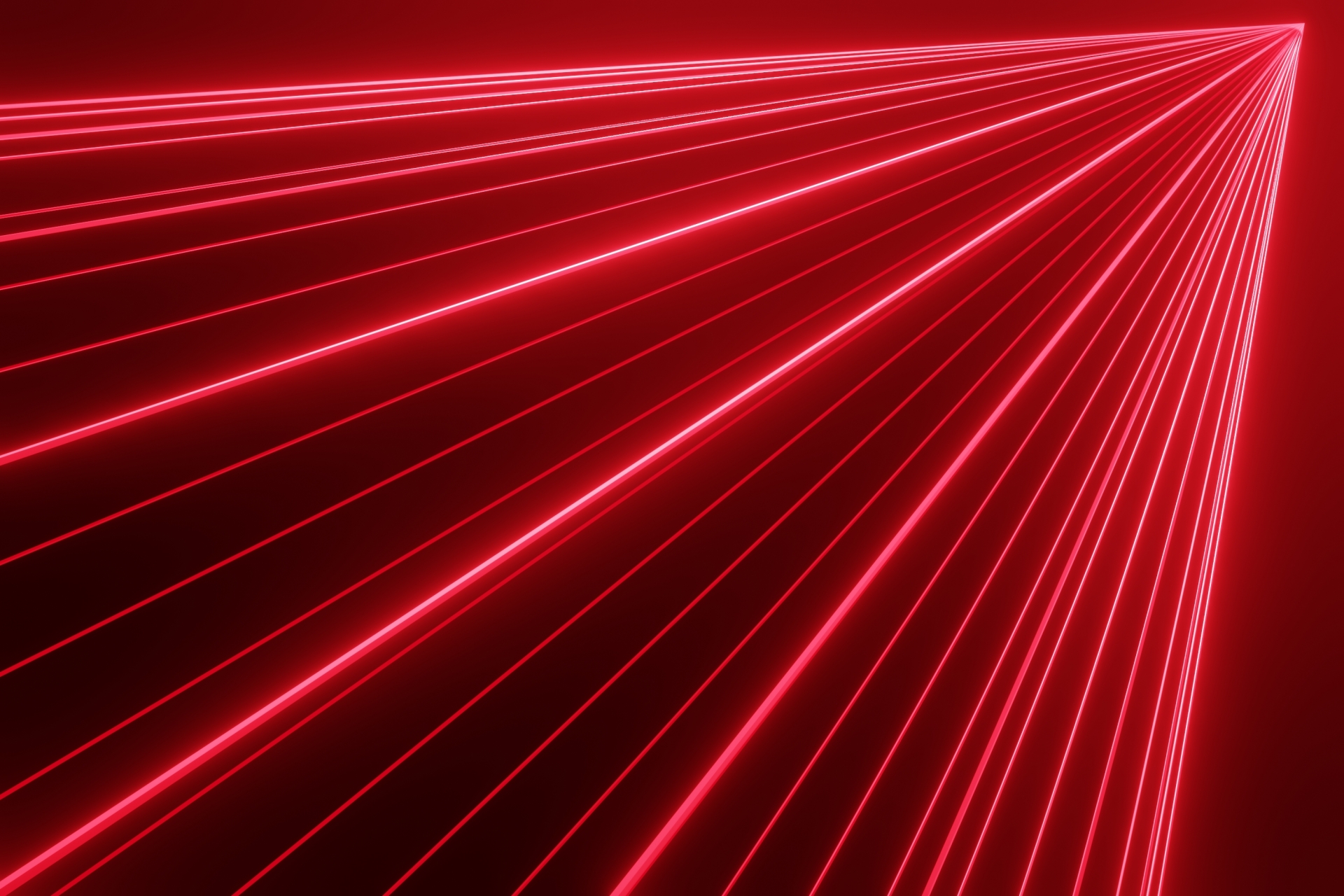
こんにちは、㈱メイコーテクノ 品質保証・商品開発担当の木村章稔です。
弊社コラム、《メタルマスクについて徹底解説》をいつもご覧いただき有難うございます。
※過去ログはコラムページをご参照下さい。
第22回目となる今回は、“メタルマスクの加工について”をご紹介させていただきます。
メタルマスクの加工方法(製法)は主に3種類(エッチング・アディティブ・レーザー)ですが、
今回はその中でも主流となっている“レーザー加工”について解説させていただきます。
『加工って言ってもどうせレーザーで切るだけでしょ?』と思われてる読者のみなさま!
実は!
何を隠そう!
・・・・・・・・
そうです、切るだけです。はい。ステンレスをカットするだけです。なんかすいません。
とは言え、その“カットするだけ”にもメタルマスクメーカーさんにより様々なノウハウがあります。
軽薄短小となっている実装情勢の中で、お客様のご要望にお応えするべく、
弊社もご多聞に漏れずこのノウハウを日々積み上げていっている次第です。
メタルマスク徹底解説と言いながら、このノウハウの詳細なところまではさすがに解説はできません。
これ解説してしまうとステンレスどころか私の給料がカット・・・。最悪首がカット・・・。
になりかねませんので申し訳ありませんご容赦ください、本当にそれはご容赦ください。
さて、くだらない長い前置きはこれくらいにしておきまして。
詳細なノウハウまでは書けませんが、メタルマスクのレーザー加工について少し掘り下げたお話をさせていただこうと思います。
それでは徹底解説を進めさせていただきます。
1.レーザー加工の仕組み
ご存じの方もいらっしゃると思いますが改めて。
メタルマスクのレーザー加工には、メタルマスク用(薄いステンレス材用)のレーザー加工機を用います。
基本的には、“すでに枠に貼り付けたステンレス材”や“専用の治具にセットしたステンレス材”など、
“テンションをかけた状態の材料”を加工機にセットします。
この材料にレーザーで穴を開けていくわけですが、レーザー光には“太さ”(弊社ではビーム径と呼んでいます)があります。
実は上から下まで同じビーム径で照射し材料をカットしているわけではなく、集光レンズによりレーザーを集約させカットしています。
虫メガネと同じですね。太陽光を通すと光が集約され、1番集光された部分をあてると葉っぱが燃える、あの原理です。
レーザーが1番集まったところの熱量を利用して材料をカットしているわけです。
またレーザー光と同軸で“アシストガス”と呼ばれる流体を一緒に射出しています。
主にエア(工場エアなど)や酸素が用いられますが、これらの“酸素パワー”をもらい“酸化反応”で熱量を上げカットしているわけです。
ちなみにアシストガスなし(レーザー光のみ)では、材料が焼けこげるだけで穴すら開きません。
このアシストガスですが先述の燃焼作用(酸化反応)の他に、集光レンズをスパッター(加工時に飛散する溶融物)から守る、
溶融金属(レーザー射出面に付着する溶融物、ドロスと言われるもの)を吹き飛ばすなど、切断性能や切断品質に大きく関りがあります。
これが基本的な“レーザー加工”の仕組みになります。
ここではアシストガスの種類や圧力がノウハウなところになるのではないでしょうか。
2.レーザー加工による開口部形状(直線性と壁面性状)
では次に、レーザーで加工したステンレス材の穴、つまりメタルマスクの開口部にあたるところがどうなるかをご説明します。
(過去コラムと重複する箇所がありますがご容赦を)
レーザーというと、レーザーポインターやガンダムのビームサーベル(たとえが昭和ですいません)のようなイメージですが、
レーザー光はずっと出っ放しにして切っているわけではありません。ミシンをイメージしてみてください。
ミシンが連続で1針1針布を貫通していくように、レーザーを1発1発射出させ材料のSUSを貫通させていきます。
その貫通穴を少しずつ重ねて開けていくことで、結果的に“材料を切断”することになっている訳です。
この加工原理が故に、その1発1発のレーザーが通った痕跡が、開口部の壁面に縦条痕となって残ります。
丸形状のレーザー光を重ねて開けていくので、この壁面の縦条痕には山の部分と谷の部分、つまり凹凸が形成される結果となります。
ものすごく簡単に言いますと、メタルマスクの開口壁面は“ギザギザしている”ということです。
このギザギザですがパルスの間隔にも左右されます。“レーザー1発1発を重ねる間隔”のことですね。
ざっくりですが重ねる間隔が広ければギザギザが粗く、狭ければ細かくなり、細かい方が開口形状の“直線性(円弧性)”は綺麗になる傾向です。
かと言って間隔が狭すぎると、材料にかかる熱量や溶融物が増え、ドロスの増加など逆に切断品質を悪くすることもあります。
また細かい話になりますが、開口部壁面の“縦条痕”はこの1発1発を重ねる間隔に加え、“加工スピード(カットする速さ)”や
“アシストガスの種類や圧力”によっても変わってきます。
このような多要素を踏まえ、ちょうど良い塩梅の設定をすることがまたメーカーの腕の見せどころなわけです。
壁面のギザギザはメタルマスクオプションの”削る処理”である”壁面処理”でも綺麗にする事が可能です。
”壁面処理”については、以下コラムでまとめてありますので宜しければご覧下さい。
3.レーザー加工による開口部形状(断面)
1の仕組みでもお話ししたように、レーザー光は集光レンズにより虫メガネのような状態で集光されています。
この光がステンレス材に貫通していくわけですが、この貫通するところを断面の観点からご説明しようと思います。
基本的にメタルマスクのレーザー加工において、レーザー光が入射するのはメタルマスクの“基板面側”になります。
基板面側からレーザーが入射し、スキージ面側にレーザーが出射される、という加工方法となります。
虫メガネのように集光されているレーザー光ですが、集光されているということは形状が“逆三角錐”になっていることになります。
この逆三角錐のレーザー光がステンレス材を貫通するところを断面でイメージしてみると、先述のレーザーの入射側(基板面側)は三角錐の広い方、レーザーの出射側(スキージ面側)は三角錐の狭い方、という形になるのがお分かりになりますでしょうか。
つまりレーザーが集光している形状(逆三角錐)であるため、開口部(レーザー貫通部)は“基板面側が広く”“スキージ面側が狭い”という、“テーパー形状”が形成されることとなります。
◎テーパーとは 「テーパーまたはテーパ (英語: taper) は、細長い構造物の径・幅・厚みなどが、先細りになっていることである。そのような設計にすることを「テーパーをつける」と言う。」
Wikipediaより引用
逆に言いますと、レーザー光の形状のため基本的には“必ずテーパーがついた開口部”になるわけです。
これが先述の“基板面側からレーザーが入射し、スキージ面側にレーザーが出射される”加工方法の理由になります。
表裏逆に加工してしまうと、スキージ面の方が広く基板面側の方が狭い“逆テーパー形状”となり、
少なからず印刷性に影響が出てしまうことになりますのでこれは要注意です。
面視を間違えてデータ作成したものを『裏返して使えば同じだからいいでしょ!』とはならないわけです。
いやそんなことしませんよ弊社。例えです例え。誤解のなきように本当に誤解のなきように。
4.意外と大事、材料のセッティング
レーザー加工機に材料をセットするのもかなり大事な要素です。
レーザー光は集光されそのちょうど良い集光具合のところでカットしていることは先に述べた通りです。
ではこの“ちょうど良い集光具合のところ”はどのようにしているかと言いますと、加工機が自動でやってくれます。
レーザーの射出口と材料との間隔(隙間)をセンサーで読み取り自動で最適な高さに調整をしてくれるわけです。便利な世の中です。
この時、材料が均一な高さにセットされていなかった場合、この高さ調整にも狂いが生じてしまいます。
またエアや酸素のアシストガスがレーザーと同軸(射出口)からブシューッと出ていますので、これにより材料が押されている状態にもなります。
これが仕組みのところで述べた“テンションをかけた状態の材料を加工機にセット”する理由です。
アシストガスの噴射で材料がブレてしまうと、せっかく高さ調整したレーザーとの距離が狂ってしまい異形状や未切断になったりしますので、
しっかりとテンションをかけブレを最小限にした状態にするわけです。
意外と材料のセッティングは重要なのです。
いかがでしたでしょうか。
ノウハウまでお話しできないので(私が色々カットされるので)若干端的にはなってしまいましたが、
そして若干純度が高めだったかもしれませんが、何かのお役に立てれば幸いです。
ちなみにご好評であればシリーズ化されるそうです(笑)
当社では基板実装におけるお客様の課題解決を目的とし、「本気のモノづくりに応える」を掲げながら日々のモノづくりに取り組んでおります。
東京、神奈川を中心に、おかげさまで最近ではモノづくりの本場、大阪や愛知からのお問い合わせも増えてきました✨
メタルマスクのことならメイコーテクノへお気軽にお問い合わせください。