メタルマスク開口部のテーパーについて
2024年03月01日時点の情報です。
先日雨の日🌧の帰り道、すれ違いざまに傘がぶつかってしまったので『あ!すいません!』と謝った相手が電柱でした、
こんにちは、㈱メイコーテクノ 品質保証・商品開発担当の木村章稔です。
弊社コラム、《メタルマスクについて徹底解説》をいつもご覧いただき有難うございます。
※過去ログはコラムページをご参照下さい。
第33回目となる今回は“メタルマスク開口部のテーパーについて”をご紹介させていただきます。
私がコラムを担当するのは実に10か月ぶりです。
以前私のコラムがシリーズ化😆✨されると聞いたのですが・・・10か月ぶりです。
なんですかね。どこからか圧力でもかかったんですかね。
とは言ってもそこまで詳しいこと、例えば社外秘などは当然記載はしていません!
まぁ何が社外秘かそうでないかは品証の私のさじ加減ですが。(←たぶんこれが原因)
あ。嘘ですよ?不安そうな顔しないでくださいね?ちゃんと守秘義務は徹底して守っておりますのでご安心を。
さて、くだらない前置きはこれぐらいにしまして、早速本題へ。
“メタルマスク開口部のテーパーについて”徹底解説を進めさせていただきます。
1.メタルマスクのテーパーとは
第22回目のコラム“メタルマスクの加工について”でも触れていますが改めて。
テーパーまたはテーパ (英語: taper) とは、細長い構造物の径・幅・厚みなどが先細りになっていることであり、
そのような設計にすることを「テーパーをつける」と言います。(Wiki様ありがとう)
ではメタルマスクのどこにテーパーが存在するのか。
すでに本コラムの題名でネタバレしていますが、そうです、開口部(穴が開いている部分)です。
メタルマスクの開口部は、基板面側からスキージ面側にかけて“先細り”の形状をしています。
実際に使用するお客様の視点で言いますと逆にした方が分かりやすいでしょうか。
“スキージ面側(はんだペーストが入る方)から基板面側(はんだペーストが抜ける方)にかけて、
裾広がりになっている”ということになります。
したがって断面で見てみますと、開口の部分が“台形”の形状になっているのです。
決してまっすぐストレートな断面形状で出来ているわけではないんですね。
ではなぜ、この“テーパー形状”になるのか。
これは工法により仕組みが変わりますので、次にそれを解説させていただきます。
ここではメタルマスクにおいて代表的な、“アディティブ(めっき)工法”と“レーザー工法”を見ていきましょう。
2.アディティブ工法でのテーパーの仕組み
ご存じの方もいらっしゃると思いますが改めて簡単に。
アディティブ(電鋳法とも呼ばれる)のメタルマスクとは、
金属の薄膜を被覆させるいわゆる“めっき”で製作するメタルマスクです。
この製作工程の中に“露光”という工程があります。
母材(基材)にドライフイルムレジスト等レジストをラミネート(貼り付け)し、
フイルムを使用して開口部のパターンをレジストに焼き付ける、という工程です。
(フイルムを使用しない直接描写の方法もあります)
※詳しくは弊社コラム“第17回目 アディティブメタルマスクについて”をご参照ください。
この露光(焼き付け)にはUV光が使用され、UV光があたった箇所のレジストは硬化します。
開口部のパターンを焼き付けるので、開口部の箇所だけレジストが硬化している形になるのです。
さて、このUV光が照射されレジストが硬化していくプロセスですが、その際図Aのようなことが起こっています。
《図A:断面から見たレジスト硬化のプロセス》
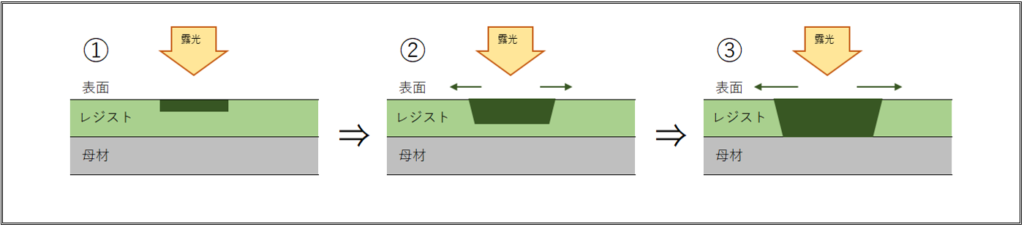
①は露光開始の時です。レジストは厚み(メタルマスクの板厚にあたる厚み)があるため、
最初はUV光照射側の表面が硬化していきます。
続いて②の段階ですが、レジストの硬化が母材に到達するまでUV光が照射され続けるため、
レジスト厚の中心に比べ、表面側の硬化がより進んで(広がって)いきます。
③の段階、つまり母材にレジストの硬化が到達するころには、UV光が照射され続けたレジスト表面側は、
さらに硬化が進んで(広がって)いき、結果硬化部分が“台形”となります。
これがアディティブ工法で開口部にテーパーができる仕組みです。
言い換えますと、レジストに露光をする以上“必ずテーパー形状になる”ということです。
私の経験則ではありますが、板厚×0.1ぐらいのテーパー量がついているイメージです。
ただしメタルマスクの特性上、スキージ面側の開口寸法<基板面側の開口寸法にしないと、
印刷性能に影響が出ますので、図Aの上側が基板面側、下側(母材側)がスキージ面側になるよう
注意してメタルマスクのデータを作成する必要があります。
3.レーザー工法でのテーパーの仕組み
先述のように、第22回目のコラム“メタルマスクの加工について”でも触れていますが、
レーザー工法とは、レーザーによりステンレスに穴(開口部)を開けていく工法になります。
このレーザーですが、上から下まで同じビーム径で照射されているわけではなく、集光レンズによりレーザーを集約させています。
虫メガネ🔎と同じと思ってください。太陽光が1番集光された部分を葉っぱにあてると燃える、あの原理です。
レーザーが1番集まったところの熱量を利用して材料をカットしているわけです。
虫メガネのように集光されているレーザー光ですが、集光されているということは形状が“逆三角錐”になっていることになります。
この逆三角錐のレーザー光がステンレス材を貫通するところを断面でイメージしてみると、レーザーの入射側は三角錐の広い方、
レーザーの出射側は三角錐の狭い方、という形になるのがお分かりになりますでしょうか。(図Bをご覧ください)
《図B:断面から見たレーザーの集光イメージ》
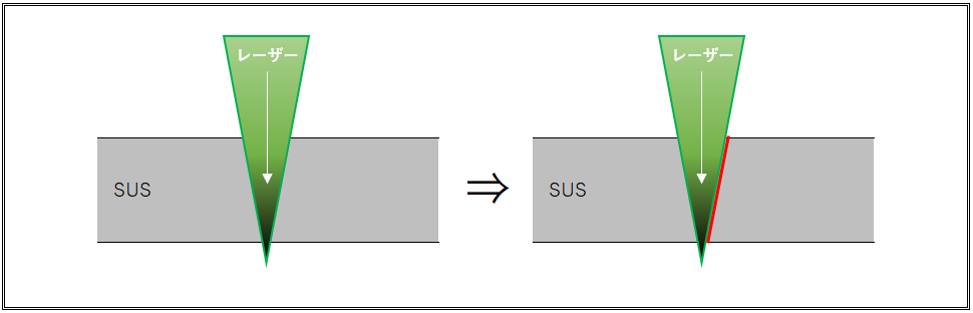
この“三角錐の広い方”から“三角錐の狭い方”へ貫通していることにより、入射側と出射側で“角度”がつくことになります。
つまり図Bの右側の図、赤い線の角度が開口部のテーパーとなるわけです。
ここまでは、よくレーザー加工におけるテーパーの説明をする時に使うイメージしやすい仕組みの説明なのですが・・・
今回はもうちょっとだけ詳しく説明を。(←圧力かかる原因)
基本的には図Bの仕組みなのですが、実はここにレーザーの“熱量”も絡んでいます。
先述のように、レーザー光は虫メガネのように集光されており、光が1番集約されているところが1番熱が高いわけです。
ということは、そこから離れるほど(虫メガネ自体に近づくほど)熱は低くなり、図Cのような状態となっています。
《図C:断面から見たレーザーの熱量イメージ》
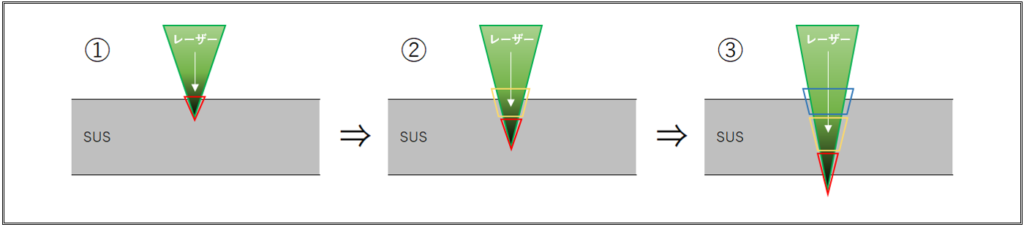
①は材料(ステンレス)へのレーザー入射時です。1番熱の高い集光点(赤枠部)から入射されます。熱が高いため切れ味バツグンです。
②の段階ですが、レーザー光が材料の奥へ入っていくと同時に、先端よりも熱の低いレーザー部分(黄枠部)が材料に当たっていきます。熱が1番高い先端で貫通させた部分を、後追いで少しジワッと熱で広げる感じです。
③の段階(先端が材料を貫通した段階)になると、更に熱の低いレーザー部分(青枠部)が材料に当たります。
①と②で貫通させた部分に、更にジュワ~ッと追いレーザーをして広げている感じですね。
先端部は熱量が大きい(高い)ため、照射の方向(下側)に向かって瞬時に貫通させることが可能です。
ただし熱量の少ない(低い)箇所は貫通方向への力(熱)が少ないため、貫通する方向へ行けない熱が横方向へ分散されます。
つまり広がる方向ですね。
簡単な説明Ver.が図B、詳しい説明Ver.が図C、これがレーザー工法で開口部にテーパーができる仕組みです。
したがって、レーザー加工をする上では“必ずテーパー形状になる”ということになります。
レーザー加工機の種類やレーザーの設定等で微小な変化はありますが、大よそ5~10µmぐらいが平均的なテーパー量のイメージです。
こちらもアディティブと同じく、図Cの上側が基板面側、下側がスキージ面側になるよう、注意してデータを作成する必要があります。
いかがでしたでしょうか。
ちょっとだけ詳しく書いた(攻めた)と思っていますが、これでまた私がコラムに顔を出さなくなったら、
『あぁ。木村やられたな🏴☠️』と何気なく察しといてください(笑)。
代わりにみなさんにとって何かのお役に立てていれば幸いです!
東京、神奈川を中心に、大阪や愛知からのお問い合わせも増えてきました
メタルマスクのことならメイコーテクノへお気軽にお問い合わせください。
今回のテーマはとてもいい勉強になりました。基本的にテーパーありきで印刷品質を管理しないといけませんね。
ありがとうございました。
FUJISAM様、コメントありがとうございます! 本コラム担当の木村です。
印刷品質は様々な要素が複合的に絡みますので難しいところとは存じますが、テーパーもひとつの要素ではあると考えております。
これからもお客様のお役に立てるような情報を発信して参りますので、引き続き宜しくお願い致します!